The aging and creep of the plastic facilitates its connection to other materials. This may cause the material on one side to expand and the product on the other side to fail. Here, a threaded plastic concrete on the washing machine is taken as an example to illustrate how to achieve the best possible design.
This article refers to the address: http://
The white goods industry is looking for cost effective and reliable manufacturing methods. The device itself should contain the fewest components. The amount of component reduction is closely related to the part that connects them, which in turn affects their useful life.
The increasing use of processing technology in the last decade has led to an increase in the use of polymers. One of the main tasks of product engineers is to find a reliable way to connect polymer components or polymer components to metal components. The most commonly used are threaded and snap-fit ​​connections, of which the former is dominant. In the design phase, engineers rely on official standards and indicators, component manufacturers or material suppliers, and especially their own experience to design.
Polymers with time-dependent relaxation and creep behavior pose a challenge to product developers. Relaxation occurs due to the presence of continuous stress, which is the result of continuous loading. Environmental effects such as temperature and humidity accelerate these phenomena.
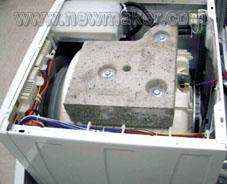
The washing machine contains a counterweight that is assembled to the polymer tub with three screws.
When considering a polymer and its associated components, the problem that engineers must solve on their own is:
â—† When and how to integrate polymer data when designing a threaded connection;
â—† How to estimate time dependence and durability to ensure the safety of the threaded connection.
Connection technology in the field of household appliances
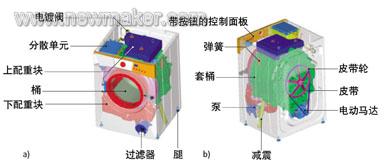
Figure 1 In order to reduce weight and save cost and energy, the main components of the washing machine are increasingly made of polymer materials.
The washing machine used here as an example has the following components (shown in Figure 1):
â—† outer casing with support legs;
â—† Includes barrels, cans, concrete weights (cconcrete ounterweights), pulleys and drive belts;
â—† A water distribution system consisting of a filtration unit and a pipeline with a dispersion unit;
â—† Electronic components including pumps, drive motors and operating platforms;
â—† Suspension system consisting of shock absorbers and springs.
Many of these components are made of polymeric materials such as pump housings, covers and most drive belts and pulleys. Dynamic and static thermomechanical stresses need to be considered when the polymer components of the washing machine and the connections between them are developed. In most cases, the way the thread is connected will be used, but snap connections (such as connections at the cover) and pin connections (such as shock absorbers) will also be used.
Moreover, the metal drum of the washing machine is now also made of a polymer material. On the other hand, the threaded connection is the main connection method. The most important connection in the tub is its connection to the concrete counterweight. In order to counteract the imbalance during the rotation process, the quality of the tub is often weighted with a concrete weight (shown in the title picture). This leads to the formation of special loads, and vibration is one of them. The challenge for product developers is to find the right way to connect polymer and metal screws and evaluate and ensure connection performance throughout the life of the washing machine.
Load the weight
In addition to quality calculations and processes, the guide VDI 2230 details the load distribution of the screws and explains the preload. Such sizing methods are usually obtained based on static loads. However, in the real world, dynamic thermomechanical loads (regular and irregular vibration/load cycles) also exist.
For this reason, self-tapping screws are often used to connect the upper and lower weights to the tub. This significantly shortens the molding time of the part and reduces the assembly cost. These measures enable the connector to withstand high loads and can be assembled and disassembled dozens of times without the quality of the connector being reduced. The purpose of using self-tapping screws is to offset (for example, clamping force/pre-stress and torque removal) the time dependence of the polymer material, where the material used is polypropylene (PP). In the VDI standard, important factors for preload change the relaxation and temperature dependence including the screw material. However, the VDI standard assumes that the joint between the components is of the metal-metal type, and after being embedded, it is considered that the preload force is reduced by about 10% and the minimum load of about 80% or the elastic limit stress of 0.2% remains at the yield point. The main feature of the polymer (threaded hub material) - time-dependent creep and/or slack, is not explicitly mentioned in the standard. In addition, only a small part of the standard is suitable for the main material of the clamping part at room temperature (so-called embedding of the contact surface, thermal expansion). The manufacturer of polymer materials therefore recommends the 100th hour during the threading of the polymer parts as a cycle during which it stabilizes itself.
Design feature
The success of this design is based on the effect of compression creep on the screw preload, which must be constant throughout the life of the washing machine for safety reasons. Where both static and dynamic load combinations exist, the life of the component is based on the fatigue limit of the polymer material.
In order to eliminate the load on the polymer material, the design of providing an additional (circular) spring washer between the screw head and the washer eliminates unwanted stress relaxation and loosening of the joint caused by dynamic loading. (shown in Figure 2). The wall thickness at the connection point of the tub made of the polymer material must be such as to prevent the screw from breaking the material with lower strength when the material is connected. As a rule of thumb, the outer diameter of a polymer part should be at least twice the nominal diameter of the screw. In addition to this, the penetration depth and the hole diameter must be proportional to the strength of the threaded connection (spinning force or release torque).
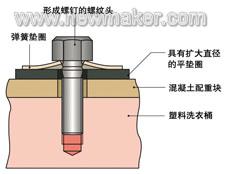
Figure 2 The threaded connection between the tub and the counterweight must withstand static and dynamic loads without loss of strength (release).
However, these standards do not fully reflect the behavior of polymers and their attachment to metals.
The probability of loosening of such a threaded connection (the assembly force FM no longer exists) is reduced by the amount FZ in which the polymer is degraded and thus the clamping member is embedded. The effective preload force FV must not be below the limit value FV, erf (shown in Figure 3) throughout the life of the product.
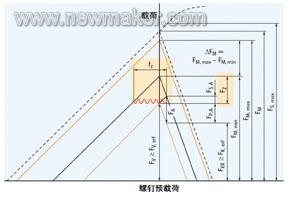
Figure 3 The general clamping force diagram can be used to read the preload force when the product is assembled and used.
The maximum helix force (FS, max) depends on the screw and its elastic properties. However, the expected load FA is dependent on the screw and the clamping member. The ratio of critical forces is calculated from the amount of stretch, which in turn depends on the hardness of the material used. In addition to the so-called 100-hour settling time, manufacturers also recommend an assembly process that uses automatic and torque sensing.
Creep and relaxation
The time-dependent behavior of polymer materials was later incorporated into the experimental estimates. An experimental total curve describes the creep as a function of time t. The curve itself is an empirical formula derived from different modulus curves at different temperatures in the same time domain combined with the displacement factor aT (shown in Figure 4). The synthetic creep tensor J(t) provides information about the preload attenuation and the looseness of the joint during product use, and is ignored at the beginning of the calculation. In addition, it is also possible to infer the life of the product (for example, aT = J(now) / J(10a)].
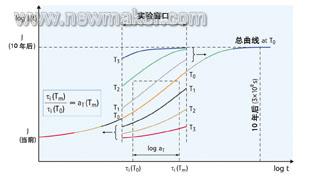
The total curve of Figure 4 J(t) is derived from the modulus curve and is related to the curve at T0 by the displacement factor aT.
On the other hand, the creep experienced by polymeric materials can also be described by a general formula for viscoelasticity:
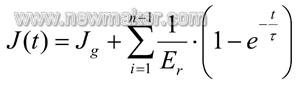
In the formula, Jg (stability time) is creep in an equilibrium state, which is produced by the connection and initial embedding of the linker. The value of the creep tensor is always increasing due to the constant load. In the present case, the barrel vibrates in various directions with a certain acceleration (due to the action of centrifugal force). The value of the acceleration depends on the style of the washing machine, and a value of 10 g (approx. upper limit of g = 9.81 m/s2) is used (shown in Fig. 5).
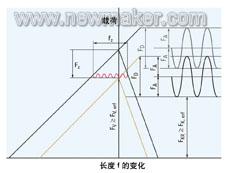
Figure 5 The dynamic load of the required clamping force on the preload force connected to the support will be reduced.
After a certain period of time, the range of dynamic loads (FA) may exceed the safety threshold of the connection and the required clamping force may not be reached. This indicates that there is a much greater vibration during use. Moreover, this may cause the connection to fail during use of the washing machine for extended life.
to sum up
When connecting at design, the following criteria must be considered:
â—† The initial creep value of the polymer material;
â—† The maximum value of the expected creep tensor and the assessment of the preload force at the end of the product service period;
â—† Characteristic behavior, corresponding adjustment and thread connection conditions of polymer under different service temperatures;
â—† The relationship between the thread connection force and the polymer material.
Adding VDI Guide 2230 with these aspects is very valuable.
The decision to unify a particular solution should not be based solely on general assumptions. It is necessary to obtain the absolute value of the creep and relaxation of the polymer, not just the relative value. However, these absolute values ​​cannot be obtained entirely by equations and simulations. In order to be able to verify the irregular and repetitive dynamic thermomechanical loads on the screws, experimental work in the actual case is necessary.
However, theoretical research results can help reduce the number of possible solutions and avoid excessive margins in selecting parameters. An optimized solution is available when experimental results and proper accelerated aging of polymer components are introduced into the design.
We are engaged in manufacturing and supplying a wide range of Transformer Bobbins which is highly used for effectual functioning. Our bobbins are manufactured using quality material such as nylon, polycarbonate and ld. These are used as suitable storage for wires in the shape of coil. Further, these are widely applicable in electronic industry and are offered as per the desired requirements and specifications of our clients.
Transformer Bobbins,Plastic Transformer Bobbins,Pot Core PC Bobbin,EFD-15 Surface Mount Bobbin,Bobbin E-Core
NINGBO BEILUN TIAOYUE MACHINE CO., LTD. , https://www.spool-manufacturer.com