Fuzzy Intelligent Realization of Heating Furnace Temperature Control System
1 Introduction
At present, the main problem of the broadband heating furnace in Laiwu Steel 1500 is uneven heating temperature and insufficient heating capacity. The actual heating capacity of the two heating furnaces is now 300-450t / h, which is lower than the design capacity of 480-520t / h (cold billet to hot billet). The temperature difference between the slab furnace is 25-35 ℃, and the temperature difference of the same slab is 20-45 ℃. The heating quality index of similar domestic production lines is that the temperature difference between the slab furnace is ≤15 ℃, and the temperature difference between the same plate is ≤15 ℃. Through in-depth investigation, it was found that the design concept of the introduced Stein heating furnace control system does not completely match the existing working conditions of Laiwu Steel, and the frequent changes of the steel rolling rhythm on site can not meet the changes of the existing working conditions, and in the actual production process The lack of necessary statistical analysis data and on-site testing methods. The production plan, heating steel type, size, billet entry temperature, waiting (stop) rolling time, and starting rolling temperature all require a period of time to slowly increase the furnace temperature to avoid a strong impact on the entire gas system, but due to With the improvement of the on-site rhythm, the operator cannot wait for the temperature to rise slowly, nor can he adjust the heating strategy in time and accurately. At the same time, it is affected by human factors (experience, responsibility, white, night shift), and the four shifts and individual operations are not uniform Long firing time will eventually cause fluctuations in furnace temperature and steel temperature, poor heating quality, high unit fuel consumption, high oxidation loss of billet, and poor product quality stability. Therefore, the Stein program cannot adapt to the actual production situation of the broadband heating furnace. Therefore, the fuzzy control theory is introduced into the heating furnace control system to simplify the original program and adapt it to the actual production needs of broadband.
2. The control of the heating furnace
The furnace body is composed of the following heating zones; preheating zone; heating zone; insulation section. Each zone is heated by burning gas and air. The combustible gas flow is adjusted according to the set values ​​in several control loops. Figure 1 is a schematic diagram of heating control:
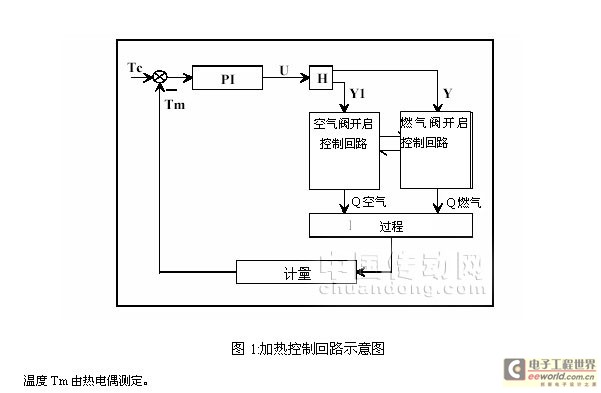
3. Traditional PID control
The output signal form of the traditional control device is as follows:

among them:
Kp-proportional gain
TI-integration time
Kp and TI are internal PI parameters, adjusted by the operator once. The output signal u (t) is converted into heating demand according to the following formula:

Among them: a, b = constant.
This value will not exceed the set limit. The «y» value is used to determine the setting value of the gas valve opening control loop. The «y1» value (air flow control loop) is calculated using the «y» value, and its purpose is to maintain the air / gas ratio within a specified time interval. The two loops are assembled using a cross control method, the purpose of which is to check this ratio. The signals that directly control the process flow are sent from these two control loops, and their names are: Q gas (gas flow rate) and Q air (air flow rate).
The system works well when the state is stable. However, the following factors can interfere with the process:
(1) Production delay (planned or unplanned), because not only will the transient be triggered at the beginning of production but also the rapid switch of the transient gas flow at the beginning of the delay.
(2) Production changes-This means that different types of products enter the furnace in turn, which means that different heating requirements are formed.
(3) The product weight in the furnace is changed and adjusted.
4. Improved fuzzy control
Introduce fuzzy control into the intelligent control system of the heating furnace. The original regulation control loop cannot exceed the limits of the complexity and uncertainty of the process, and the proportional integral control device (PI) cannot correctly control the development of the process. Disturbance in production changes, pacing changes, products (type, size, quantity), the use of different production methods (short delay, long delay, low flame) and other factors all cause conversions, which was not carried out in the original regulation Considered carefully. Through the transfer function of the process and the field experience of the operator, the coefficients of the proportional integral differential control device (PID) of the complete process are obtained. Calculate the coefficient of the control device with standard adjustment formulas, combine the parameters of the mathematical model of the process with the parameters of the control device, and the operator's experience parameters to realize the adjustable control of the PI parameters, and find the speed of the control loop With a precise balance point, it can meet the requirements of different production rhythms of broadband steel.
Using fuzzy management procedures, the traditional PI (proportional integral) parameters determined by the control device according to actual operation. The data is extracted from system observation, experience and process understanding to form a special database of fuzzy logic management procedures. The fuzzy logic block determines and adapts the necessary changes determined by the proportional integral control device according to the input value.
The schematic diagram of the system is shown in Figure 2:
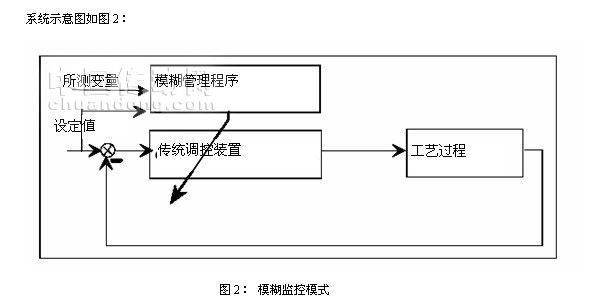
The fuzzy regulation is a monitoring level regulation. During the regulation, the parameters of the proportional integral differential regulation device are calculated online. The regulation device is used to measure the temperature of the standard control loop. The variables considered are the set value; the measured temperature; the measured temperature variable within a specified time step; the instantaneous regional load; the actual fixed step value.
The fuzzy control stage can be connected or disconnected with a simple on / off command. If the fuzzy control stage is disconnected, the proportional integral differential parameter is the default value set in the traditional way.
In order to ensure normal operation, the fuzzy logic controller requires data as input variables described by the fuzzy subset; error; the kinetic data of the measured temperature; the weight of the product in this section; the actual fixed-step speed; the output of the fuzzy subset description; Proportional gain: Kp; integration time: Ki; type rules.
The schematic diagram of fuzzy block principle mode is shown in Figure 3:
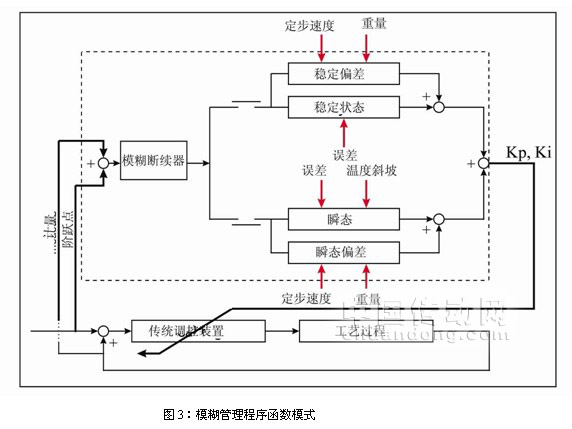
The fuzzy controller has two modes: "steady state mode" and "transient mode". When the measured value is not far from the set value, we think the system is in a stable state (fuzzy reasoning). In the steady state, the adjustment of Kp and Ki is done through temperature error. When the error is too large, we assume that the system enters a transient state. In this case, it is necessary to dynamically control the measured temperature to be consistent with the response of the furnace. The change of working mode is completed by the fuzzy interrupter, which will ensure a balanced transition from one mode to another. Through these models, we can get the initial values ​​of Kp and Ki. In the second mode group, these values ​​will be adjusted, and the deviation of Kp and Ki (weight and pace speed) in the actual working condition function will also be calculated. Finally, the intermediate results of the steady state and transient mode groups will be used.
5 Conclusion
The use of fuzzy control makes the system control more reliable and stable, the temperature error is significantly reduced, and an excellent control effect is obtained, which provides a guarantee for the subsequent rolling process, reduces the steel pile, and greatly improves the economic benefit.
In 2017, Touchwo
Launched brand new advertising equipment with touch function,adapted Samsung.LG. AU.etc industrialGrade lcd/LED display panel from all over the world famous brand.with top-rated decoding technology,playing
1080P full HD more fluently and perfectly.
Base with screw design in the floor mat to suit for all kind of grounds ( install wheels is optional)
Led Interactive Advertising Player
Touch Screen Wall Display,Lcd Advertising Player,Lcd Digital Signage Display,Led Interactive Advertising Player
Guangzhou TouchWo Electronics Co.,Ltd. , https://www.touchaio.com